HDPE vs. Concrete?
Innovation is all around us. It’s in the sky with aviation, it’s ground level with cars, and it’s underground with your wastewater pump stations. For years, performance cars like hotrods were built with steel frames and bodies. Since the turn of the century, automakers have been transitioning to carbon fiber builds because carbon fiber is stronger, lighter, and built to last much longer than its steel counterpart. Similarly, in the pump station wet well field, high density Polyethylene (HDPE) has become the more efficient wet well material compared to the traditional concrete. But do the HDPE efficiencies truly bring the benefits versus the tried and proven conventional precast concrete option?
What is HDPE?
HDPE wet wells are a polyethylene commodity that have been growing in popularity within the wastewater industry. Made from a string of ethylene molecules, this thermoplastic is ideal for wastewater applications because it’s naturally Hydrogen-Sulfide (H2S) resistant without the need for any additional coatings. Additionally, it has a 100 year design life making it a once in a life time update. An HDPE wet well is manufactured and delivered as a monolithic structure. Not only does this prevent any leaks or infiltration, but it also gives the packaged pump station provider the ability to pre-plumb the wet well so it’s site-ready.
What is Concrete?
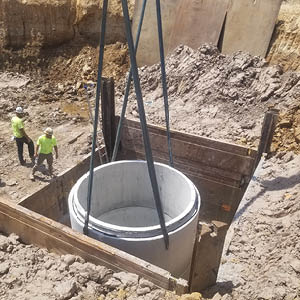
Concrete wet wells are the most common wet well type within the pump station industry. Traditionally, concrete is made from a mixture of cement and water with aggregates such as sand and gravel or crushed stone. The cement and water make a paste that acts as the bonding agent that keeps the concrete together. This also makes concrete porous and over time, this gives opportunity for cracks and fissures to develop creating a leak path. Sewage gassing off creates H2S (Hydrogen Sulfide) which accelerates the breakdown of concrete. Furthermore, concrete wet wells are built from individual concrete rings that arrive separate to the site. The water resistance of the wet well is reliant upon the rings being sealed correctly. This is a task performed by the contractor on site. Good contractors work diligently to ensure a set of field-stacked concrete rings receive the necessary sealant to provide years of leak-resistance, but each joint is a potential risk point of leakage, if not today, then one day in the future. This not only goes against EPA regulations but can cause lasting environmental damage to the area.
For years concrete has been readily available. This is part of what made it the most used solution for pump station wet wells. However, as of March 2022 the General Services Administration of the United States government set carbon limits on concrete for federal projects. This has slashed the concrete reserves by almost one-third and made concrete generally more difficult to get. To compound that, the design life of wastewater concrete wet wells is generally shorter with the installation beginning an important maintenance routine to get maximum design life. While a general design life we see with wastewater concrete wet wells is roughly 20 years with treatments, many concrete manufacture warranties only last 5 years at the most. This leaves you with a product you’ll need to replace more often with a material that is increasingly harder to get.
H2S Corrosion
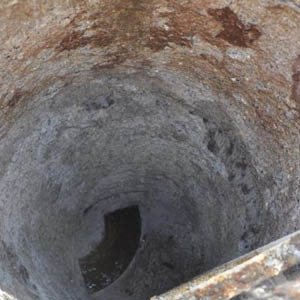
Hydrogen sulfide is a destructive gas that provokes acid corrosion. Dissolving in water, it creates a weak acid that causes pitting in the vicinity of oxygen or, more commonly in wastewater, carbon dioxide. From there the gas eats away at concrete walls of a wet well. In wastewater applications, pump station designs with long force mains provide ample time for the wastewater to go septic. Once septic, it gasses off leading to hydrogen sulfide production and H2S corrosion. This is also an issue in repump stations where wastewater pump stations don't discharge directly to a treatment plant and make a couple stops in lift stations along the way. Currently with the trend towards lower water consumption systems, wastewater retention times have increased, causing it to go stagnant and create H2S. H2S is the lingering villain of any concrete and a sanitary pump station frequently becomes a prone to that environment.
Concrete Treatments
To extend the life of a concrete wet well against H2S and other outside elements, treatments can be applied. These treatments can range from add-mixtures, paints, epoxies, and more. While these treatments may protect against corrosion for some period of time, the longest warranty we've seen on the market is only good for 10 years. Also, many of these coatings are applied while a worker endures a confined space entry situation. As referenced in our Six Ways to Eliminate Confined Space Entry in Pump Stations post, in the United States alone, between 2011 and 2018, over 1,000 workers died from occupational injuries involving a confined space.
Concrete Add-Mixtures:
Additives added to the concrete during the batching process can help protect against H2S. These add-mixtures can delay the effects from corrosion often seen in typical concrete but does not stop the process completely. With it being mixed in with the concrete, there isn’t a way to replace.
Concrete Paint Coatings:
Bituminous paint is an architectural mixture made from the distillation of crude oil, bitumen. While it works great in highway and nautical applications, it requires re-coating and maintenance to ensure the barrier remains intact. If that coating wears thin and is compromised in any spot, deterioration occurs quickly.
Concrete Epoxy Coatings:
Epoxy sealers are two component paints that can provide an active barrier when coating concrete. Like with most of the coatings we’ve discussed, this again highlights the maintenance requirement over time. Unfortunately due to the nature of a wet well, often a compromised coating is only discovered after the deterioration has begun.
Concrete Polyurea Coatings:
Polyurea is spray-applied within a wet well once the wet well is installed. The spray forms a solid monolithic layer within the wet well similar to a pickup truck bedliner. Although this can be a premium product effective in providing H2S corrosion resistance and extending the concrete's lifespan, it's comparatively expensive to apply. Additionally, groundwater can still push through the concrete and in some cases deform the polyurea coat.
While all these coatings work as solutions, they are all temporary fixes. Depending on the application, many of these treatments will need reapplication roughly every 2 for paint to every 10 years for Polyurea coatings.
Wet Well Calculations
All structures installed in excavations require measurements to be taken to prevent floatation. These include anti-floatation calculations to determine the size of an anti-floatation ring. Buoyancy calculations determine the requirement to prevent a structure from floating or shifting upwards in high groundwater conditions. All wet wells have an anti-floatation flange at the bottom of the wet well. A concrete wet well may require a smaller anti-floatation flange to prevent the floatation while HDPE typically has larger. This is because HDPE weighs a tenth of an equally sized concrete piece. For any HDPE wet well application, we provide buoyancy calculations as shown below. Based on the wet well diameter and depth we provide a flange with safety factor assuming the water table is at grade. This provides you with the peace of mind knowing that once your HDPE wet well is in the ground, it’s staying put.
For a more detailed breakdown of how to size a wet well accurately — including peak flow, emergency retention, and pump cycle calculations — see our wet well design calculations guide.
Loudoun County Pump Station (ASTM 1759) |
|
|
|
Wet Well Seismic Capabilities
Seismic capabilities are calculated by taking the vertical load on the wet well and dividing that by the wet well and soil stiffness. This gets your deflection percentage. In general, all plastic piping is designed to be flexible. This flexibility allows HDPE to come unharmed through unharmed seismic events like mild earthquakes or the freeze-thaw effect of the seasons. A space where seismic design might not always be top of mind but is of large concern is railways. According to the American Railway Engineering and Maintenance-of-Way Association (AREMA), one train passage can generate a tremor with the energy output of a magnitude 1 earthquake and can be detectable for up to 60 miles from the track. Now imagine the wear and tear that comes with thousands of those tremors per day. The rigidity of concrete makes it a lot more difficult for a wet well to withstand the punishment brought along by outside forces.
Installation Process
When installing a pump station wet well there are many variables to factor in. How long will there be an open excavation? An open excavation can lead to dewatering issues. It can also be costly to rent the large crane equipment as well as the skilled hands required to install the wet well in the excavation. What size trench box is required? Depending on the location, space could be tight and make the install difficult.
HDPE Wet Well Installation
An HDPE wet well arrives to site as a prefabricated monolithic structure complete with guide rails and piping. It’s able to accomplish this because HDPE is about one-tenth the weight of concrete. Surprisingly, the design limitations of HDPE wet wells usually come down to road laws for shipping the product to site. We limit the size at 11 ft. I.D. and 50 ft. deep simply because of shipping requirements from state to state. Regardless, complete installation can take place in a single morning or afternoon with the excavator used to dig the hole for most wet wells. The video below shows the installation of an 8 ft. diameter by 23.5 ft. HDPE wet well for a new housing development in Southwest Ohio.
* As a note, the distance between the excavation and roadway required this particular install to be done by a lifting crane, but typically, an excavator is sufficient.
Concrete Wet Well Installation
Concrete is heavy. Because of this weight, concrete wet wells are delivered to site as individual concrete rings. During the installation process joint sealant is stuck to the top of each of these rings. Unfortunately, this also brings in a variable to the effectiveness of the pump station. If the sealant is installed in an improper fashion, the seal becomes compromised, and the pump station is prone to leakage. The video below shows the installation of a 10 ft. diameter by 27 ft. deep concrete wet well for a hospital in the Cleveland, Ohio area. In total five truckloads of concrete rings were required to complete the 27 ft. of depth.
* As a note, this wet well still required the guide rails and piping to be installed separately along with an H2S corrosion prevention coating application that needed to be completed on another date.
Wet Well Costs
The first cost you see on an HDPE wet well is higher than the cost of raw concrete precast. Let’s break down a typical price comparison using a 6 ft. diameter by 26 ft. deep wet well as an example. A typical HDPE wet well come to $30,438 compared to a concrete at $8,609. But what exactly are you getting for that additional investment? The HDPE arrives at site as a monolithic structure, fully fitted out with all the guide rails and piping, ready for installation. It can be installed in one pick and backfilling can take place immediately. Concrete wet wells arrive in multiple rings that take multiple picks and a much longer time to install. Needing a larger lifting crane to account for the extra weight means more rental time and specialized labor that gets added to that $8,609. On top of that, piping and guide rails need to be field installed after a concrete wet well is set. This adds to on-site installation time which is costly for the contractor and end user as they prevent the project from being completed.
Line Item | Concrete | HDPE |
Base Wet Well | $8,609 - $12,000 | $30,438 |
Concrete Admixture | $650 - $1,000 | N/A |
Basic to Advanced Interior Coating | $1,000 - $10,000 | N/A |
Joint Wrap/Sealant | $2,000 - $3,500 | N/A |
Shoring Rental | $1,000 - $1,500 | $1,000 |
Dewatering Costs | $1,000 - $1,500 | $750 |
Crane for Concrete | $1,000 - $5,000 | N/A |
Mechanical Plumbing Labor | $4,500 - $6,500 | Included |
Total: | $19,759 - $41,000 | $32,188 |
Time to Complete | 3-5 Days | 1/2 Day |
* As a note, all prices beside the base wet well are estimates.
We hope this gives you a better understanding of how for a similar cost, HDPE can deliver a faster, easier, and superior wet well, with substantially longer design life and eliminate multiple job site risks. If you're in the early planning stages, try our Wet Well Design Calculator to estimate sizing based on your flow rate and project specifications
To learn more about innovations in the pump station industry, check out our blogs on NoVault™ Pump Station Design vs. a Conventional Pump Station or Factory Preassembled vs. Contractor Field Assembled Pump Station. If you have any questions on your next pump station design, contact us today!