Frequently Asked Pump Station Design Questions
The design phase is the most important part of any project. It’s the ideal and most cost effective time to fix flaws of a project's design. In a packaged pump station this can include hundreds of choices for you or the engineer make. That’s where we come in. We’re pump station experts with more than 30+ years of pumps and pump station experience. We’re here to manage your complete pump station in a prepackaged solution. We ensure your pump station’s success from start to finish with our three-step Design, Build, Maintain approach. Reviewing a pump station project together early in the design phase helps select the ideal equipment and answer challenges in a wholistic manner, with the full scope of the project in mind. Check out some of the most common questions we get when working with engineers and contractors and how we go about bringing peace of mind with our solutions.
Advantages of Pre-Packaged Pump Stations
What are the advantages of a pre-packaged pump station?
If you know the basic site conditions, a pre-packaged pump station is the ideal answer. Excel makes it easy to enter parameters and get the benefit of the experience of thousands of pump stations successfully designed, built, and maintained. Suggestions from our in-house design team, assistance with engineering, dedicated project management professionals, extensive capacity in manufacturing, assembly, and factory testing ensure the pre-packaged station is a seamless experience.
How long does it take to get a quote for a pump station?
Upon receiving a pump station request we will respond within 24-48 hours to gather any project specific data and define any unique scope requirements you might have on the project. From there our typical proposal response time is within one week for budgetary and bidding projects.
What information is required to size a pump/pump station?
In order to a size a pump and/or a pump station and provide a proposal we typically need a site plan drawing with elevations, flow rates (both average daily flow, peak flow rates, and any emergency storage requirements), hydraulic force main profile details, and electrical service information.
Can EFG provide buoyancy calculations and structural calculations from a certified professional engineer?
Yes, third party engineering calculations can be provided for any wet well type (HDPE, Fiberglass, Concrete). The only question is to determine what phase of the project we provide these. We’ve found it’s best to the overall project and provides the preferred wholistic approach if these are discussed early on during the design phase or pre-construction phase. However, these calculations can be provided at any time throughout the process.
How long does a submittal package take?
Typically, providing a submittal package can take 3-4 weeks. Up to two weeks can be added whether or not third party engineering calculations are required, or nonstandard electrical or generator needs have to be met. The advantage of an Excel Pre-Packaged Pump Station is that the submittal package is fully complete with all components of the pump station for one review by the engineer. This is much more efficient than individual reviews of the pump station components breaking out pump submittals, wet well submittals, controls submittals, and others.
Can you size a pump station for our project?
Yes, we have a certified wet well sizing calculator that we use on every pump station project to ensure you’re getting the exact pump station you need. We cover our process in our How to Design a Submersible Wastewater Pump Station blog.
Are CAD drawings available?
Yes, all our design files are created in SolidWorks as 3D models to scale and can be exported into any common format requirements. These include AutoCAD, eViewer, Revit, .SLDDRW, .SLDPRT, .SLDASM, .DWG / DXF, .STEP, .jpg, .pdf, .eDrawings (for viewing and measuring), and more.
What are the benefits of modeling in 3D?
We use SolidWorks while designing pump stations. This helps us ensure our digital drawings match up with what's manufactured by our production team, making everyone on the same page. The video below will show how the information gets from the sales team to the design team, and how the design team then works in lockstep with the production team.
Determining the Right Pump & Pump Station
How do you determine which pump is best suited for a specific job application?
Pumps are used in a wide variety of applications, from sanitary wastewater, to stormwater, to potable drinking water, not including a plethora of industrial manufacturing uses, however, the simplest place to start is to determine what fluid needs to be pumped. Additionally, the gallons per minute (GPM), total dynamic head (TDH), and static head need to be confirmed to assist in finding the best pump for a specific application. If you don’t have all the details required for a pump selection, get in touch with us and we can often advise what’s typical for an application and how to verify the selection is correct. When replacing an existing pump, often there are upgrade options to consider as well.
What are the key deciding factors when choosing a particular pump type for a pump station? Non-clog, chopper, or grinder?
The design flow rate, force main size, wet well design, electrical service, and solids content in the pumped media are key deciding factors in making a pump selection for a pump station.
What is the difference between a pump station, lift station, and booster station? Are they interchangeable?
A pump station and a lift station both require a wet well below ground to collect wastewater or stormwater, and these two names are commonly interchangeable. Other common names we've seen include sump pump station and ejector pump, which are also interchangeable with lift station. A booster pump station isn’t interchangeable and is specifically used for potable drinking water distribution systems where water pressure is low or for filling water towers in remote areas.
How many pump stations can one control panel handle?
It depends on the application. One master pump station can control up to 5 stations from a central location. This would include the master pump station and up to 2-4 slave pump station control panels as part of a project. It can be accomplished to whatever the end user desires but we have seen it be cost prohibitive and needlessly complex to design a control panel this way. Our experience is that it’s typically with each pump station having it’s own control panel, even if it’s a basic one.
Does "Wet Well" mean there is always water in the bottom of Pump Station?
Yes, submersible pumps require minimum submergence to operate efficiently and not become airlocked. We use a transducer with float back up controls system to ensure minimum submergence is maintained.
What are the best applications for HDPE vs Concrete vs Fiberglass as my wet well choice?
HDPE and Fiberglass arrive at the site prefabricated, tested, and ready to install. Fiberglass has a 40-year design life and is H2S resistant. HDPE ups the ante with a 100-year design life and is inert to H2S corrosion requiring zero additional coatings. Both are good for sanitary wastewater applications and HDPE is double walled which is a requirement for Leachate applications. These are some of the newer innovations in the wet well market, where concrete is the most common within the industry but has the shortest design life and often requires the most maintenance to avoid any faster deterioration.
Pump Station Structures & Environments
Does every pump need a fiberglass or concrete wet well structure? What do the fiberglass or concrete structures do?
Yes, every sanitary or stormwater pump station requires a vertical or horizontal wet well to collect water and ensure there isn't any backups or sewer overflows in the collection system. This wet well provides storage capacity and a working volume to ensure pumps are not running constantly, which could lead to premature failure.
Does soil type/environment conditions/location ever play a part in determining which wet well basin material type?
Groundwater infiltration or groundwater level does impact what wet well type is best suited for a given application. Soil conditions should be considered, especially if there is risk of contamination. In an application where the soil is poor, an HDPE or Fiberglass wet well provides resistance to corrosion without requiring an exterior coating. There are other distinct advantages of each wet well type, and our design team is available to discuss this further. For example, concrete structures under the ground have seams that must be sealed and maintained against leaks. Monolithic structures such as HDPE or fiberglass are preferred for applications with groundwater, however, the main factor in this decision is client or engineer preference.
What's the benefits to the Aluminum NoVault™ compared to similar fiberglass above grade enclosure designs?
The NoVault aluminum enclosure is fabricated from structural tube and sheeting to a mill finish of ASTM 3003 that includes a structural floor or base plate in the design to eliminate water intrusion. This design is more robust and durable, providing maximum protection to components inside with insulated protection, and is not subject to UV damage or extreme weather events. Additionally, the piping and controls are brought to eye level and give ease of use accessibility for the operator.
Control Panel Submitted on is a NEMA 12 rating, but it should be NEMA 4?
NEMA 4 and NEMA 4X rated enclosures offer somewhat more advanced levels of protection than NEMA 12 enclosures. They offer protection against water, external ice, foreign object ingress, and more both indoor and outdoor. We get this question in regards to our NoVault pump station design and if the NEMA 12 aluminum control panel will be all right in the elements. The control panel in a NoVault will never fully be in the elements as it's insulated and gasketed gull-wing doors that provide enclosed protection and a wall mounted electrical radiant heater that's thermostatically controlled for freeze protection.
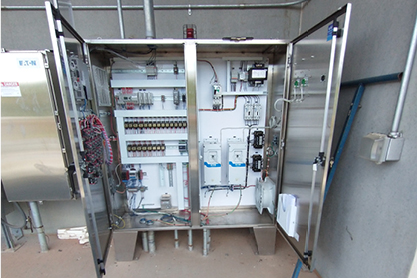
We hope this helps give you a better understanding of what the Excel Design Experience is and where Excel Fluid Group can benefit in your next pump station design. To get further design information, check out our NoVault vs. Conventional Pump Station Design and our Which Pump Station Design is Right for You? blog posts. If you have any questions about your next pump station design, contact us today!