Submersible Pumps vs. Self-Priming Pumps?
Push or pull? It can get really embarrassing when you walk up to a door and try the wrong one. Lucky for you, when designing a pump station, you have an option of either. Self-priming pumps are a surface mounted suction lift design that pull wastewater from the bottom of the wet well up into the station above. They are kept outside the liquid, typically within a structure such as a pump house, and driven by an electric motor or a combustion engine. Pulling can work just fine in many situations but if you’ve ever walked up to a pull door with your hands full, you know it’s not always ideal.
Submersible pumps are immersed within the wet well or tank with a motor and pump combination installed below grade. They push the liquids from the bottom of the wet well and up and out of the pump station. To keep the door metaphor, put your back into it to open it with your hands full.
Design Limitations
Pump stations designed for submersible and self-priming pumps are set up differently with each having their own characteristics and limitations. For a long time, submersible pump stations were set up with a separate below grade valve vault or dry well. This would be where check valves, piping, plug valves, and more would be placed below grade where maintenance personnel would be subjected to confined space entry dangers and regulation. To combat this, Excel Fluid Group designed the NoVault™ pump station enclosure which brings all the valves above grade into a small shelter and eliminates the risk of typical confined space entry. Additionally, with the pump at the bottom of the wet well, submersible pump station designs can theoretically have an unlimited depth. This is because submersible pumps push the wastewater and don’t have the physical lift restrictions.
With self-priming pumps being above the liquid designs, there are physical limitations that prevent the pump effectiveness above 20 feet. The 20 feet is measured not from grade but from the centerline of the pump shaft to the off level in the wet well. The physical limiting factors on Earth only allow a maximum of 14.7 PSI of atmospheric pressure at sea level. The higher up in elevation and altitude a pump station is placed, the less atmospheric pressure there is available to us. Self-priming pumps use suction lift with air pressure to suck the liquid into the pump. It’s important to remember though, there is a difference in theoretical suction lift and practical suction lift. To start with we need to convert PSI into Feet. The conversion is 2.31 feet to 1 PSI or an optimal 14.7 PSI X 2.31 ft. = 33.95 ft./h of water column measured as vacuum. While we can get close, absolute vacuum is impossible to achieve on Earth.
This brings us to “practical suction lift”. No pump operates in a perfect world, and tolerances must be applied to allow the pump to work and pass wastewater. This impedes the ability for the pump to suck up the peak 33.95 ft. Most pump manufactures will not endorse the installation of their products into applications over 20-23 feet as this allows the self-priming design some ability to “wear” and still be able to perform. Added to this is the limitations within the pump itself and measured as Net Positive Suction Head Required (NPSHR). The self-priming pump manufactures publish a NPSHR curve that changes based on the flowrate. As an example in Figure A, this manufacture states that the NPSHR at 400 GPM is 11 ft. at 2000 RPM. This 11 feet must be subtracted from the 33 feet that is available (33 – 11 = 22 feet). The 22 feet is measured and is described as Net Positive Suction Head Available. Most self-priming pump manufacturers would not endorse the use of this pump model in an application above 15-18 feet of lift. It is challenging to find a pump with a NPSHR of less than 5 feet at any flowrate. Additionally, in most self-priming pump stations, you will find that the wet well depth is no more than 20 feet deep. These inherent limitation with self-priming pumps cannot be improved upon, simply due to physics.
Figure A:
When pumping wastewater self-priming pump stations can quickly lose their priming ability as the grit and nasty material causes their tolerances to open. This can often lead to a station losing 3+ feet of suction lift within its first year in operation. This must be taken into account when designing a self-priming pump station.
With these design limitations, why are self-priming pumps still selected over submersible pumps? Much of the answer lies in the improvement of reliability in submersible pumps. Maintenance teams historically worried about accessing submersible pumps down in the wet well, so felt more comfortable with self-priming pumps up in a shelter. Submersible pumps reliability and efficiency has become the industry standard with motor technology and advancement in seals. Lifting or access systems and plug in cords make it easier than ever to pull pumps and perform maintenance. They are also quieter and require less area above ground. While self-priming still works, the benefits of submersible seem to be way of the future.
Wet Self-Priming Stations
Self-priming stations are mainly broken up into two general designs, wet prime and vacuum prime. In a wastewater application, a wet prime station uses an impeller that works as a liquid ring vacuum pump. In Figure B below, you can see the impeller location is eccentric to the pumping chamber and uses the liquid held in the chamber to draw the air out of the suction pipe and water in. However, it can take minutes to create this vacuum and allow the pump to start pumping. The motor is forced to run to create the vacuum but also must run for several minutes pumping zero gallons per minute. This can be very inefficient and costly as your motor is running, but you are not pumping a drop. A wet self-priming pump utilizes the water in the pump to create the vacuum, so it is designed with the suction port high up to retain the water when it shuts off. To further expedite the priming process a suction check valve is used to help retain the water in the casing. Upon initial startup the operator must fill the casing with water.
Figure B:
Vacuum Self-Priming Stations
A vacuum self-priming pump sucks the air out of the suction line, utilizing an external device. There are many ways to accomplish this. Some manufactures use an air compressor and Venturi. Some others will use a shaft powered diaphragm pump as shown in Figure C, while even others still will use an electric motor driven vacuum pump. Because vacuum prime pumps use a very efficient, purpose-built vacuum system to draw the water into the pump these vacuum assisted pumps can start up in seconds, unlike their wet self-priming counterparts.
Figure C:
Self-Priming Side Effects
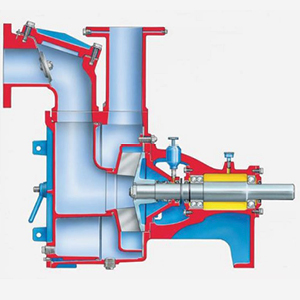
Pump Familiarity
Once a pump station is operational, it’s always important for maintenance crews to be familiar with the system. An above grade hoist is often required for pulling submersible pumps up a rail system for maintenance. While there are a number of lifting devices available, one industry innovation is the electric hoist in the Excel NoVault pump station. We designed the lifting hoist to come standard in our NoVault and have other hoist options available for other submersible pump station designs. In total, about 95% of the submersible stations we design either have a lifting hoist or have provisions to add a hoist at a later date.
Self-priming pump stations are easily accessible because they are set up above grade. However, as a result of this, typically no self-priming stations have a lifting hoist provided. This can cause difficulties when the removal or maintenance of the pump needs to take place. We have had customers complain that the pump stopped priming and found that the suction pipe was plugged. That required maintenance personnel to climb down into the wet well to fish out the clog at the bottom of the suction pipe in the wet well. The confined space entry concerns are only exemplified compared to a submersible pump station. Submersibles with a lifting hoist allow for the pump to be pulled out and serviced above grade. Additionally, self-priming pump stations typically have very small hatch doors, limiting the personnel that can physically access inside the wet well.
Maintenance
No matter what pump station you have, maintenance is important. There are countless parts and pieces that are put through their paces to make any pump station run. We recommend using our Maintenance Plus program on an annual, semi-annual, or quarterly basis because our team is well versed in both submersible and self-priming pump station maintenance. However, we also understand that many pump station owners have their own maintenance crews. In our 30+ years of experience, we have found priming maintenance technicians are traditionally more versed in mechanical machine techniques. Conversely, submersible maintenance technicians are typically more versed in both mechanical and electrical pumping technologies and have a more diverse and complete skillset. This means typically a submersible maintenance technician could service both a submersible and self-priming station while priming maintenance technicians often can only handle a self-priming station.
Overall, we have also found self-priming stations to require more care than their submersible pump counterparts. A large amount of time and effort is put into monitoring grease and oil levels on a self-priming pump. Without lubricated bearings, pumps are eventually going to seize up and fail. Submersible pump bearings are permanently lubricated inside the pump because they are filled at the factory and designed and enclosed to never leak. Additionally, self-priming pumps require an abundance of adjustments throughout its lifetime. These include constantly monitoring tolerances like the impeller and volute clearances because if they open too wide, the pump won’t prime and becomes useless. Keep in mind, without a lifting hoist most maintenance and upkeep is done crouched down in a doghouse type enclosure typically near ground level. This can be a killer on any maintenance personnel’s knees and cause wear and tear on the body and station.
Lastly, clogging can be fixed in two ways: clearing or preventing. Clearing happens when the pump gets clogged. In a submersible pump, if the pump gets clogged you bring it up with the lifting hoist, look into the pump inlet and clean it out. For a self-priming pump, you first must take the pump apart to confirm that the clog is not in the pump. If no materials are found, then you must check the length of the suction pipe for any debris. Not only is this more to check for a simple fix but, you have the added issues of confined space entry in the wet well. To prevent clogging, wastewater handling pumps can be set up with chopper or submersible grinder designs which combat the solids traveling through the waste stream.
Wastewater Handling Designs
Water saving appliances like toilets, dishwashers, and washing machines are great in concept. In practice though, water saving appliances put a strain on waste streams by creating higher concentrations of sewage. More and more there are foreign objects getting into waste streams that have no business being there. We’ve seen greatly marketed flushable wipes, not be so flushable. Additionally, cloth materials have increasingly been flushed causing monumental clogging issues. Don’t forget, this is all on top of natural solids already in the waste stream. Any of this can and does wreak havoc on a standard pump system. Because of this, pump companies have been forced to research and innovate their products with solids handling, grinder, and chopper designs.
Grinder and Chopper Pumps
Chopper and grinder pump designs each have the same goal. The concept is to get solids smaller so there is less of a chance of clogging in the pump or through the waste stream. The way this is accomplished between submersible and self-priming pumps, can greatly differ. Typically, a submersible grinder pump is used in lower flow rate pump stations while a chopper pump is best for higher flow rates. This is because a grinder pump is applied in lower flow applications that utilize small diameter force mains requiring high pressure. Chopper pumps typically are utilized with force mains greater than 4 in. and flow rates greater than 100 GPM.
Self-priming chopper pump options are extremely limited and aren’t available in all pump sizes. Self-priming grinder pumps do not yet exist on the market. This is a result of the chopping done at the pump impeller on a self-prime design. This leads to a vulnerability of solids potentially clogging in the suction pipe and causing detrimental damage very quickly. Conversely, on a submersible pump design, the chopper blade is set at the inlet of the pump. This means there is no pipe any solid must travel through in the pump station before it is pumped.
Lastly, in general, the submersible pump industry embraced the grinder and chopper concept much earlier than the self-priming industry did. Because of this, grinder and chopper designs and add-ons are widely available for most any size and submersible design on the market. The self-priming industry was slower to adapt to the approach, so the availability is limited depending on design and size.
We hope this helps give you a better understanding of what pump design is right for your next project. Check out our blogs on What Affects Your Pump Station’s Cost? and How To Design an Efficient Pump Station to learn more. If you have any questions on your next pump station design, contact us today!