How To Achieve Pump Station Efficiency
When we speak of the efficiency of any machine, we are referring to how well it can convert one form of energy into another. Much like a car, there are a lot of different parts of a pump station that can lead to an efficient, and more importantly, an inefficient design. Selecting the right components to design your pump station solution can lead to easy gains of efficiencies that can help your operational budget. Finding the right size and storage volume for your pump station wet well can put your pump in its best place to succeed long term. Electronic components like variable frequency drives (VFDs) help your machine work smarter, not harder. Lastly, if the “pump” in a pump station struggles to handle the materials flowing through it for your application, it will not performance at its peak. We want to cover how Excel Fluid Group can help you tackle pump station efficiency for your specific applications.
Why Pump Station Efficiency is Important
Pump stations are an asset to any community although they are not always viewed as such. When viewed only as a cost or expense, the entity is forfeiting the chance to impact the design and create the most efficient solution for their needs. When designed correctly, a pump station will become an asset to any community and provide future growth and deliver residual benefits for the area.
For starters, investing in an efficient pump design can lead to cost savings long term over the life of the pump station. This can come from a variety of different ways. Like an energy efficient light bulb, when designed correctly, pump station solutions can use less power overall that lead to a lower energy bill for the community. This efficiency comes from designing and selecting from a holistic viewpoint, specifically for your application. While it may sound counterintuitive, for some solutions it can be better to buy less efficient pumps for cost but gain efficiencies with clog resistance, proper wet well size, and pipe design and materials. The efficiency is gained back when you include manpower and labor costs to maintain a less efficient pump, compared to a more efficient pump. This is why when getting a pump station designed, it helps to put things into context for your needs. Pump station solutions must be based on the industry and functionality of your uses.
Ways Piping Can Help Pump Station Efficiency
Pipes are the highways of a pump station. Like with highways, the size of a pipe and the material it is made from can play a major role in the outcome. However, also like roads the elevation, terrain, and end points are usually defined and not likely to be changed.
Inside Diameter of Force Main Pipe
Using the right diameter sized pipe can be instrumental in gaining or losing efficiency in your overall pump station design. Moving through these force main pipes can be everything from fresh water, all the way to solid laden liquid. At minimum, you want liquids within your pipe to be moving at a rate of about 2.5 feet per second. If a solid laden liquid moved too slow within the pipe, the solids can settle out within the piping. Think of it like cholesterol within your veins. The more they are constrained, the higher pressure needed to pump the same amount through. This can lead to the pipes needing to be cleaned out through a costly pigging or a jetter process.
Use the Correct Pipe Material
Using the right material when selecting your force mail piping is a very influential part of your pump station’s efficiency. The pipe material selected can directly affect the pipe’s C-Factor (coefficient of friction). In conjunction with the Great Lakes – Upper Mississippi River Board (GLUMRB), the EPA’s C-Factor requirements for piping materials date back to a time when pipes were primarily made from rougher materials like clay or iron. With advancements in technology, nowadays it is common practice to use materials like HDPE, PVC, and ductile iron when designing pump station piping. These materials are smoother than the previous piping materials and therefore have the lowest C-Factor and the least amount of friction loss.
HDPE Piping
HDPE piping has the lowest C-Factor while also having the highest level of ductility. Think of the HDPE material as a super flexible wet noodle. In the summers and winters when the ground expands and contracts, HDPE piping has the ability to move with it. HDPE is very abrasion resistant and able to convey rough materials such as small rocks and sand. Lastly, the material is available on a roll for quicker and easier installation. However, HDPE piping sizes do not follow standard imperial measurements and require caution while applying.
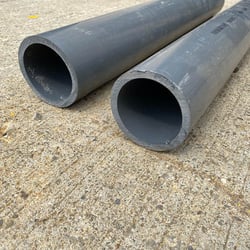
PVC Piping
PVC piping is non-corrosive and has the same C-Factor as HDPE piping. However, it is less flexible and more brittle than the standard HDPE piping. PVC is more commonly utilized in smaller diameter applications.
Ductile Iron
While ductile iron does not have a C-Factor quite as low as HDPE and PVC piping, it is still widely accepted within the industry. Ductile iron piping is extremely rigid and sturdy. However, this rigidity can be challenged in harsh environments with ground movement in freeze and thaw. In addition, ductile iron piping must be protected for corrosion and abrasion resistance.
What About Piping is Out of Your Control
There are certain aspects of force main design that are usually set in stone. Piping layouts are usually set up for pumping from point A to point B. In addition, elevation and static head challenges can be tricky to find solutions for. It is not usually within budget to change the terrain when creating a piping layout. The length and rise of elevations are the constants to remember and design for when creating your efficient pump station.
Importance of Wet Well Size or Storage Volumes
The wet well size of a pump station can affect how much wear and tear a pump station goes through. If your wet well is too small, not only is the well more prone to overflow, but the pump will also run too often and burn itself out prematurely. If your wet well is too big the increased retention time can lead to biological problems such as sewage going septic and causing increased odors. In addition, if the waste is kept within the wet well for too long, it can turn into gases that eat away at materials like concrete, ductile iron, and more. This is why retention time in the wet well and retention time in the force main pipe must be considered when designing your pump station solution.
How to Find the Right Size Wet Well
When looking for the correct wet well sizing for your pump station design, you must first think about the maximums and minimums the station will experience. A pump should have a maximum of eight starts per hour. Anything more is inefficient and can wear out the pump quicker. To determine the minimum and maximum number of starts per hour you must figure out the average daily flow (ADF) and peak daily flow (PDF). In the example of a housing development, the peak daily flow would happen in the morning while most are getting ready for work or at night when people get home. However, the wet well and pumps will be needed less overnight and during midday when there is less activity. The average daily flow is determined by dividing out usage out over a 24-hour period.
Ultimately, when figuring out your wet well sizing, you are aiming to try to have a safety factor that just avoids overflows and backups. Ideally, you want the pump to be resting three times the amount that the pump is on. Resting the pump three times its average run time will help to not overwhelm and prematurely wear out the pump. Wet well sizing is critical for the pump station’s longevity and the overall lifecycle costs.
How VFDs Can Increase Pump Station Efficiency
Using electronic components like a variable frequency drive (VFD) can help flatten the curve between your peak daily flow and average daily flow. In the example above where a housing development is used more in the morning than overnight, VFDs can help control the pump flow automatically to pump more during peak time than during off-peak times. This will help combat any extremes when figuring out wet well sizes while also giving you peace of mind knowing that your pump is smart enough to handle what comes its way.
In addition to working within extremes, VFDs also can provide savings to your power bill by only giving the output needed at that moment. To put it simply, VFDs match supply with demand. Why run your pump 100% on when only 33% is needed? These savings not only lead to lower power bills but also help reduce wear and tear on pumps, valves, and piping.
While VFDs sound like they are complicated and expensive to set up, advancements in pre-programmed settings allow for economical and easy setup with seamless upkeep. Our NoVault™ Pump Station solution primarily comes complete with an ArcSentry™ Control Panel with a PUMP Vision Controller that provides access of wet well levels, flow monitoring, and automatically shows the VFD speed for reference.
How to Combat Clogged Pump Efficiency Lost
The “pump” in a pump station is the heart of an efficient design. Efficiencies in piping material tie back to less friction throughout and a pump having to work less to experience the same outcome. Wet well size and storage volume helps the pump not get overworked and makes sure it is used correctly. Electronic components like VFDs are programmed so the pump meets its appropriate demand. All of this can be centered around the pump output but what happened if you do not have the right pump for the application?
All wastewater pumps should be designed for handling solids of some sort. A lot of focus is often placed on the hydraulic efficiency of the pump setting aside ability for the pump to handle the products in the waste stream. A pump that is clogged will naturally have longer run times, lead to excessive wear, and then can become subject to a catastrophic failure. That is why the GLUMRB requires a minimum of a three-inch solids handling pump for any wastewater solution. Like mentioned previously, a three-inch minimum could lead to a lower hydraulic efficiency but provide clog resistance and operational consistency. Pumps that stay in operation without the added costs of maintenance labor allow for a lower cost of ownership.
Grinder pumps were originally designed for lower flow rates and smaller diameter piping. Most grinder pumps range from one to 150 gallons per minute and often utilize 1.25 inch to three-inch piping. Grinder pumps typically have hardened stainless steel blades with vortex impellers to create a sewage slurry reducing possibility of clogging.
Chopper pumps are designed to chop solids in challenging wastewater applications which are becoming more commonplace in the waste streams of today. These choppers are often applied in pump stations above 80 GPM and force main piping larger than three inches. The cutting system uses a slicing action that limits clogging and reduces the costs associated with pump maintenance. A chopper pumps doesn’t always have the greatest hydraulic efficiencies but can provide outright efficiency in not having to allocate resources to repairs and replacements while increasing the pump’s overall lifespan.
Selecting the right chopper or grinder pump for your solution all varies based on your application. Hotels, truck stops, and jails have harsher wastewater with foreign solids compared to a residential areas or business parks. Using the right chopper or grinder pump for your application can have outstanding effects and complete your efficient pump station.
We hope this helps give you a complete approach of the variety of ways Excel Fluid Group can help positively impact your pump station’s efficiency. If you have additional questions about water and wastewater pump stations, contact us today!