Frequently Asked Pump Station Build Questions
After the successful design of a pump station, the reward comes when it turns into reality. As a trusted partner, Excel Fluid Group manufactures solutions specific to your design requirements, budget, and manage the project to fit your timeframe. Our pump stations are built with a wholistic approach. This means that we’ll assist with design, build to spec, and test the pump station performance before it arrives to you at the site. Our processes manage the execution of the project and keep your team informed. It’s a streamlined solution from a single source, with in-house project management services, and value-engineering capabilities that minimize risk. With the project relying on timely execution, we get a lot of questions from contractors and developers about what they should except working with us. Check out some of the most common questions we get and how our continued efforts to bring peace of mind are achieved.
Pump Station Lead Times
What are the factors that can affect a pump station's lead time?
There are a variety of factors that can affect a pump station’s lead time. The three most common we see are vendor product delays, submittal documentation delays, and site condition delays. The vendor product delay is when a vendor simply doesn’t have the product available in a timely manner. We will reference our supply chain experience and work with you to find an equal or comparable replacement if and when these issues come up. We are proud of our working relationship with of our vendors and often get priority to acquire the specified products needed. A submittal documentation delay is when the engineering team needs more time than expected to review and verify the product meets specifications. Our experienced project management team works tirelessly to consolidate submittals for efficient review and respond promptly using an engineer response form to any questions or clarifications requested. Additionally, this can be done by setting up a virtual meeting to review in a collaborative space, ultimately expediting the review process. When we see a site delay, it’s typically when conditions have slowed down the project and the site is not ready to receive the pump station. In this scenario, once the product is complete, we can keep the packaged station in our stock yard until you’re ready to receive it on site.
What is the standard pump station lead time?
Leadtime can vary depending on the type of project. We will work with you during the submittal process to confirm the pump station design and start sourcing verified materials when further details are yet to be established. After approval our typical lead times are:
Wet Well Type
- Most wet well types (concrete, fiberglass, HDPE): 8 – 12 weeks
- Exceptions for special designs, concrete coatings, and any additional concrete liner needed
Pump Station Design
- Conventional design with separate valve vault: 12 – 16 weeks
- NoVault™ design: 12 – 16 weeks
- Custom Prefabricated Building: 26 – 30 weeks
Our robust ISO9001 certified team will handle fabrication of wet well, pump station, and controls simultaneously throughout the build process.
What do you do to alleviate pump station lead time pressure?
The COVID-era lead times have been tough on everyone. We work to alleviate some of that pressure by stocking as many parts and components as we can (including HDPE and fiberglass wet well, NoVault enclosures, piping, control panels and more), have a broad network with a variety or vendors, and have in-house ISO9001 manufacturing capabilities with a UL508A and UL698A Certified control panel shop, HDPE fabrication, and more.
Will you keep in contact with me during the pump station project build?
Of course! We assign a dedicated single point of contact (project manager) on every project with a cadence of weekly meetings (where applicable) to provide you with updates through the pump station build process.
Pump Station Construction
How do you ensure that every component in a prefabricated pump station fits as required?
When we design pump stations in SolidWorks, it allows us to check design inferences digitally before our prefabricated pump stations are built and sent to site. The benefit of building thousands of pump stations over the last 30 years gives us insight into high risk areas of final fit and finish.
What steps are taken to ensure I received exactly what was promised in the submittal?
Following our design process where we solidify the components of your pump station, every project we complete follows our 9-step build process. This process ensures you’re going to receive what is agreed upon from the submittal process.
-
Raw materials sourced: This is where we get all of the materials required to build your pump station from trusted vendors, suppliers, and partners.
-
Build the enclosure (NoVault™, prefabricated, etc.): Whether it’s a prefabricated enclosure or one of our NoVault pump station designs, we prepare the enclosure to be ready for the coming components.
-
Mechanical is installed within the wet well: The piping, valves, and supports and built into the enclosure.
-
Electrical is installed in the pump station: Electrical controls are assembled and placed inside the enclosure.
-
The pump station is factory tested before any necessary components leave our facility: This tests that the pumps work as intended with the control panel, electrical and communication systems work as designed, piping is set up as needed, and any other checks required.
-
Wet well installed: When using an HDPE or fiberglass basin, the wet well will arrive to site ready to set in the excavation with the necessary piping. In the case of concrete, the rings will get installed, joints sealed against leaking, and treated as needed before field-installing any of the piping.
-
Flat top set: When using a NoVault pump station, the polymer concrete flat top arrives to site with the access hatch and safety grate preinstalled. Polymer is inert to H2S corrosion and it allows for fast and easy installation, but must be positioned level. The other option is a field poured concrete flat top. We see this used often with our custom prefabricated enclosures.
-
The pump station is delivered and installed: This is when the prefabricated enclosure arrives. In cases with a NoVault, polymer concrete flat top, and an HDPE or fiberglass wet well, the entire pump station wet well to enclosure can arrive onsite ready to install.
-
Pump station start up is completed: The start up is simply a retest of our factory test at Step 5, ensuring that everything still operates as agreed upon.
Does EFG offer factory testing with witness capabilities?
As mentioned above, testing is step 5 of our 9 step process. It's literally central to every pump station built. When testing occurs, visitors to our Cleveland, OH facilities are welcomed. If onsite inspection isn’t convenient, our project managers will provide our findings after testing to all required parties.
Pump Station Installations
I’m tight on space, near a roadway, creek, and property line. What is the best way to get a pump station on a compact footprint?
Our recommendation for a compact pump station is the NoVault enclosure mounted on the wet well as this removes the underground valve box typically provided in a traditional pump station design. This can also be provided on a riser to ensure the valves and controls are above the 100-year flood levels. The NoVault has operator safety and service convenience included, in addition to its compact footprint.
What equipment will I need at the jobsite to unload/install a Fiberglass Pump Station?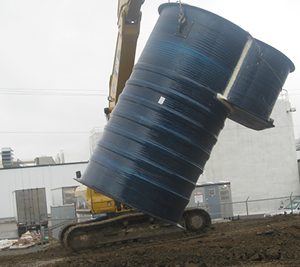
As a rule of thumb, when installing a fiberglass pump station, we recommend using the same equipment used during the excavation process. Typically, if it can reach the bottom of the excavation if can handle the weight to install it. A 3 ft. diameter by 10 ft. deep pump station can weigh as little as 890 lbs. On the other extreme, 10 ft. diameter by 40 ft. deep HDPE pump stations can weigh over 19,000 lbs. We're happy to provide general weights for shipment and installation for any of your pump stations.
What equipment will I need at the jobsite to unload/install a Polymer Concrete Flat Top?
Polymer concrete flat tops will arrive to site with the hatches, chain hooks, float and upper guide rail brackets installed. From there, make sure the equipment you're using is able to pick up the flat top level (minimum 84 in. x 84 in. and maximum 126 in. x 168 in.) They can weigh between 2,570 lbs. and 9,000 lbs. depending on the size of your pump station.
What equipment will I need at the jobsite to unload/install a No Vault Pump Station?
The NoVault arrives to site with the control panel and valve piping prefabricated. You can pick the enclosure with an excavator, forklift, or any other machinery rated for lifts over 2,500 lbs. (for the NV2) and 3,500 lbs. (for the NV3 and NV4). For the NV2, use the lifting lugs at the top of the station and for the NV3 and NV4 use lifting bars that slide through the floor of the station.
On the Scope of Work, it says "Installation by Others". Can Excel not install my pump station?
We manufacture the pump stations that are the easiest to install of any manufacturer. We will support the installation process with world class drawings and installation guides. When required, we can even go onsite to provide oversight and guidance. We do not typically install the station in the field.
Who does Excel Fluid Group recommend to install our pump stations?
We have a large nationwide network of contractors that have successfully installed our pump stations. We are confident we can recommend someone in your area with experience installing packaged pump stations.
Pump Station Start Up
What do I need to do for you to come start my station?
In order to perform start up on a pump station the pumps and control panel must be installed and connected, the station must have incoming power, the level controls are set, and there is water in the wet well to test the station.
We hope this helps give you a better understanding of what the Excel Build Experience is and where Excel Fluid Group can benefit in your next pump station project. To get further design information, check our Answering Your Pump Station Design Questions and Factory Preassembled vs. Contractor Field Assembled Pump Station blog posts. If you have any questions about your next pump station design, contact us today!